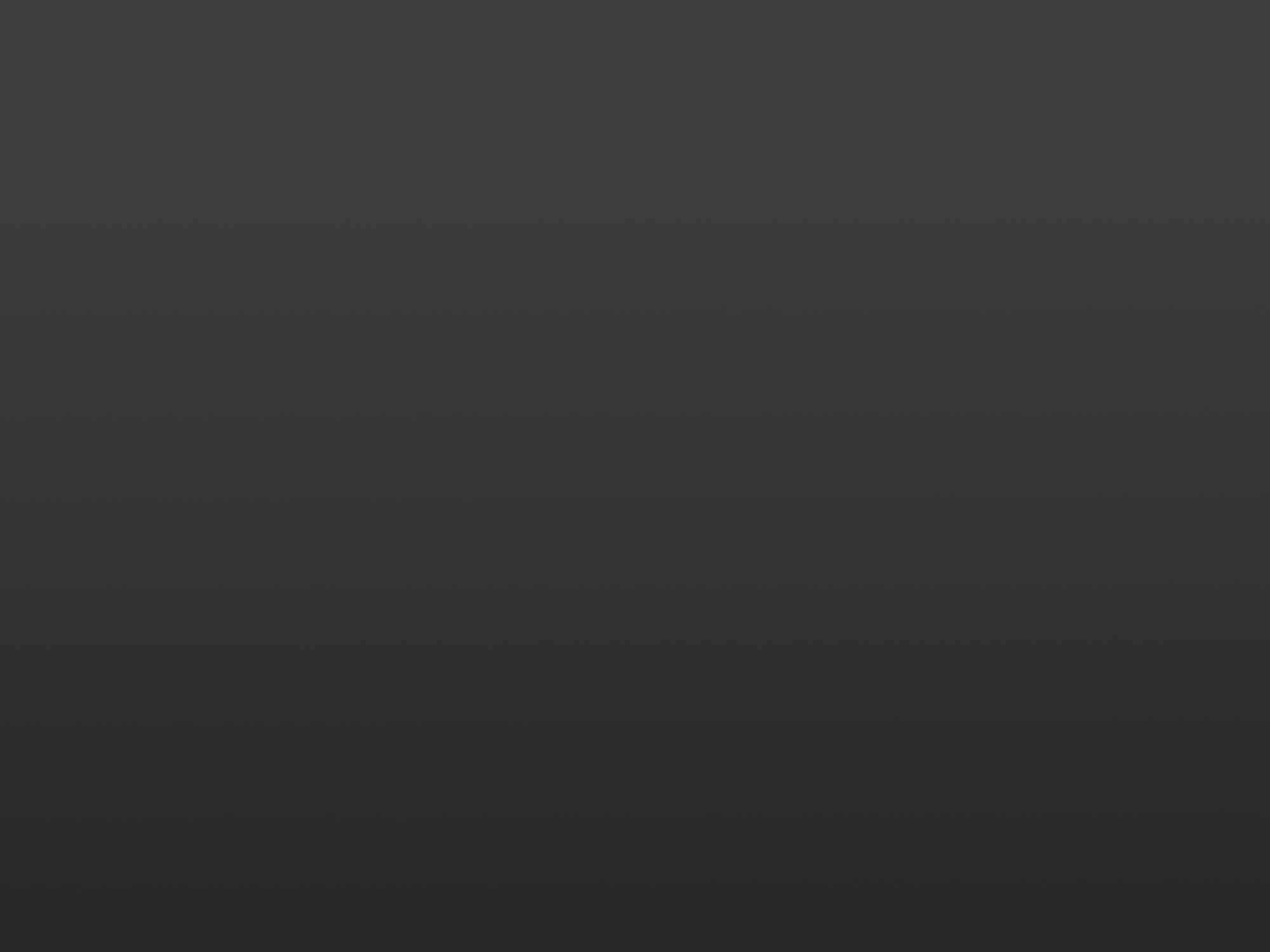

BUILDING A HANA: WINDING THE COIL
1: WINDING THE COIL
The process of winding ultra-fine 4N copper wire onto a cross coil attached to a cantilever within a fixed magnet is crucial for generating electrical currents. The tension and placement of the wire are meticulously controlled to optimise signal generation, and this precise winding is vital to the performance of HANA moving coil cartridges. The cantilever is mounted and wound with copper wire, ensuring all four legs of the cross coil are wound identically to maintain both electrical and mechanical balance, and here is an excerpt explaining how this occurs.
Skilled technicians use specialised tools to wind ultra-fine copper wire onto the cross coil, which is attached to a cantilever. This cantilever moves within a fixed magnet, generating electrical currents. The tension and placement of the wire are meticulously controlled to ensure uniformity, a critical factor for optimal signal generation. The precise winding of the cross coil is fundamental to the performance of all HANA cartridges.
Using a specialised coil-winding machine, the suspension cantilever is mounted and wound with high-purity 4N copper wire, which is only 15 microns thick. The technician carefully threads the wire, and the machine winds the coil, counting precisely each turn.
This process is repeated until all four legs of the cross coil are wound. Ensuring that all four legs are wound identically is vital to achieving electrical and mechanical balance. Once completed, the coil is coated, removed from the jig, and placed carefully to rest until the next stage of assembly.